Aluminum and Alloys
Creating parts for aerospace and automotive applications requires the highest level of precision and accuracy of cut and fit. Your final product needs to be smooth and ready for use in critical components of airplanes, vehicles, and other mechanical and technical applications.
With so many moving parts, like proper weld practices and choosing the right alloy, deburring can come as an afterthought. Don’t let the end of your process slip by without the same rigorous standard of excellence that you apply the rest of the production.
The burr
Experienced fabricators understand the necessity of deburring after cutting aluminum, whether slicing off the edge or creating a hole. It can also be time-consuming, frustrating and, if using the wrong tools, a waste of valuable time and materials.
There are many schools of thought on the best methods for deburring aluminum. It really depends on the scale and precision of the product you are fabricating. For aerospace and automotive applications, precise deburring is key to both safety and aesthetics.
Read this scholarly article for an in-depth look at the burr formation and deburring processes.
Important considerations in deburring:
- Properties of Aluminum
Understanding aluminum and its alloys will help you to prevent highly obtrusive burrs in the first place- Aluminum is valued in aerospace manufacturing due to its high strength to density ratio, as mentioned in this overview of Aluminum’s competitive edge
- Aluminum’s malleability causes it to create burrs easily
- Properties of burrs
The aforementioned scholarly article on deburring points out the importance of knowing the properties of burrs in order to choose the best method for deburring. The four major properties of the burr to examine are:
- Location of burr – A burr on an edge of a piece versus a burr in a drilled hole require different methods and tools for removal
- Length of burr – Similar to location, the length of the burr
- Number of edges to be deburred – Making sure your process is sustainable throughout the duration of removal is a consideration here
- Size and Height of burr – Burrs are often classified into five categories based on obtrusiveness, which can be a significant factor in choosing the best deburring tools and technique for your burr
Four Common Deburring Methods – Pros and Cons
- Manual deburring
- Pros: Still the most widely used deburring application, quick, and easy to adapt
- Cons: Also the most prone to errors as it is frequently performed by non-qualified operators
- Robotic Deburring
- Pros: Very precise, accurate, and fast deburring
- Cons: Expensive and time consuming to set up
- Brush deburring
- Pros: Considered fast, safe, and effective
- Cons: Several environmental, health, and safety concerns arise from the dust and particle emissions produced by the brush method
- Bonded abrasive deburring
- Pros: Versatile method for heavy stock removal
- Cons: Short lifetime, dust, and possible new smaller burrs
- Abrasive jet machining
- Pros: Removes material from work parts using a high-speed stream of media particles through a nozzle by gas
- Cons: Dust collection chamber is needed
Deburring Aluminum
Deburring aluminium after cutting is not cut and dry. It requires attention to the type of burr and selection of the best deburring method for the burr.
The major side effects of deburring methods on aluminum work parts may appear on dimensions, tensile residual stress, smut, discoloration, surface passivation and generation of new burrs.
– Deburring and edge finishing of aluminum alloys: A review, 2013
Manual deburring is a very fast way of removing the sharp edges after a cutting application. Cotton Fiber Mounted Points can remove burs quickly without changing part geometry. There is a cushion action that comes with using Cotton Fiber.
It is very adaptable to the task at hand and saves time. If using this method for deburring you can choose also different sized/shaped mounted points to fit in holes or smaller cutouts.
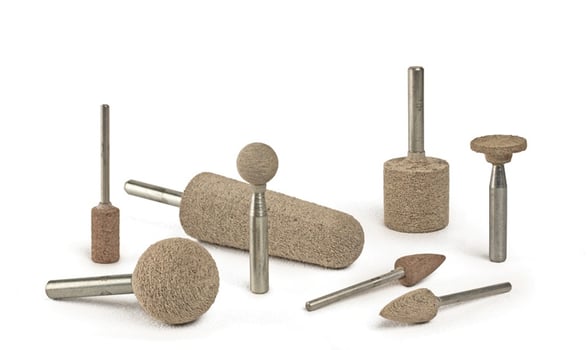
As mentioned previously, the real difficulty is ensuring the operators are well-trained to perform the deburring. Solution: train your operators in the proper safety and techniques for manual deburring, starting with a brief introduction video to the process!
To see precision manual deburring in action, watch this instructional video below:
Deburring is a necessary component for aluminum products, so make sure you and your team stay up on the deburring processes that fit your manufacturing standards.
If you are looking to upgrade your manual deburring or implement robotic deburring, contact our experts here for advice.